Optimiertes Störungsmanagement durch Workflow-Unterstützung
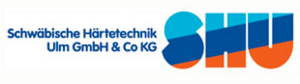
Die Schwäbische Härtetechnik Ulm GmbH & Co. KG (SHU) ist eine der größten inhabergeführten Lohnhärtereien Deutschlands. Als ISO/TS zertifiziertes Unternehmen verfolgt die SHU einen kontinuierlichen Verbesserungsprozess (KVP). Störungen in der Produktion frühzeitig zu erkennen und zukünftig zu vermeiden, ist deshalb ein wichtiges Anliegen der SHU. Um Störungen an ihren Härte- und anderen Anlagen zu erfassen und zu bearbeiten, setzte die SHU in der Vergangenheit auf eine gewachsene Lösung aus „Office-Bordmitteln“. Durch die Einführung des Störungsportals von AristaFlow gelang es, das Störungsmanagement erheblich und nachhaltig zu vereinfachen.
Kommentar schreiben